Primero se debe comenzar con la definición de “mantenimiento” ya que es la base de esta filosofía.
¿Qué es el mantenimiento?
Es la actividad humana que garantiza la existencia de un servicio dentro de una calidad esperada con acciones que tienen como objetivo preservar un artículo o restaurarlo a un estado, en el cual pueda llevar a cabo alguna función requerida. Estas acciones incluyen la combinación de las acciones técnicas y administrativas para una correcta ejecución.
Acciones del mantenimiento:
Personal calificado para la realización del mantenimiento
Herramientas especializadas para el mantenimiento
Software y un sistema de gestión del mantenimiento
Planes de mantenimiento preventivo
Gestión y disponibilidad de refacciones y materiales de mantenimiento
Beneficios de mantenimiento:
Elimina o minimiza defectos en productos
Elimina o minimiza condiciones inseguras para los empleados
Aumenta y mejora la disponibilidad de los equipos productivos
Minimiza los costos asociados al mantenimiento
Tipos de mantenimiento
Correctivo: Su aplicación se realiza cuando un equipo por motivo de alguna falla esté detenido por completo debido a esta causa. Generalmente este tipo de mantenimiento es muy costoso por los impactos en la productividad (MANTENER)
Preventivo: Su aplicación se realiza cuando un equipo por motivo de alguna falla esté trabajando parcialmente. Generalmente este tipo de mantenimiento es muy costoso por los impactos financieros en refacciones (CONSERVAR)
Mantenimiento correctivo (<1900) | Mantenimiento preventivo (>1900) | Mantenimiento predictivo (1950) | TPM (1970) |
Se realiza cuando el equipo falló por completo. Al ser una actividad no planeada se tiene tiempos muertos no presupuestados. Debe ser realizado por personal capacitado. | Se realiza antes de que el equipo falle. Se basa en planes de mantenimiento ya establecidos. Su realización puede ser planeada y presupuestada. Debe ser realizado por personal capacitado. | Se realiza antes de que el equipo falle. Se basa en los resultados de las mediciones de los equipos predictivos. Su realización puede ser planeada y presupuestada. Debe ser realizado por personal capacitado. | Se realiza antes de que el equipo falle. Se basa en planes de mantenimiento ya establecidos. Su realización puede ser planeada y presupuestada. Debe ser realizado por los mismos operadores de los equipos. |
Antecedentes de TPM
El Mantenimiento Productivo Total o TPM en sus siglas en inglés (Total Productive Maintenance), tiene sus orígenes en los Estados Unidos, donde las empresas aplicaban ciertas prácticas para prevenir fallas y con ellos, impedir acontecimientos no planeados o reparaciones de emergencia.
Durante la post guerra mientras Japón reconstruía su economía, varios ingenieros japoneses visitaron estas plantas para tomar ideas y llevarlas a su país natal. Fue con Nippodenso, una fábrica proveedora de partes para Toyota, donde se aplicaron los conceptos de mantenimiento básico a todos los empleados y no solo a los especialistas en mantenimiento.
¿Qué es Mantenimiento productivo total?
TPM es parte del mantenimiento preventivo de los equipos, combinado con la metodología de mejora continua que permite a los equipos operar de manera continua, eficiente y dentro de los estándares de calidad bajo los conceptos de:
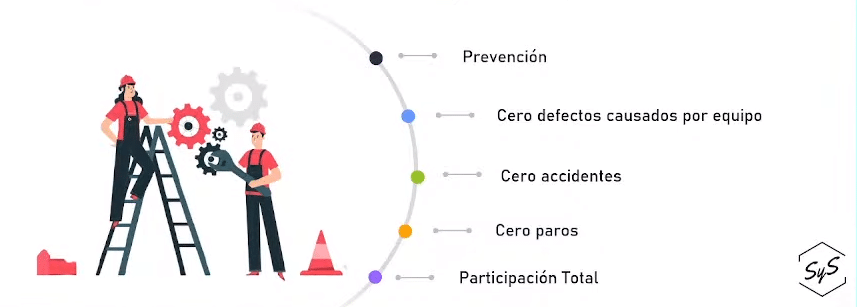
TPM involucra a los operadores de los equipos como apoyo en el mantenimiento, llevando a cabo rutinas de limpieza, inspección y mantenimiento menor, mientras el personal de mantenimiento se concentra en actividades especializadas del propio mantenimiento del equipo.
Actividades de TPM
Las principales actividades a realizar en el TPM son las siguientes:
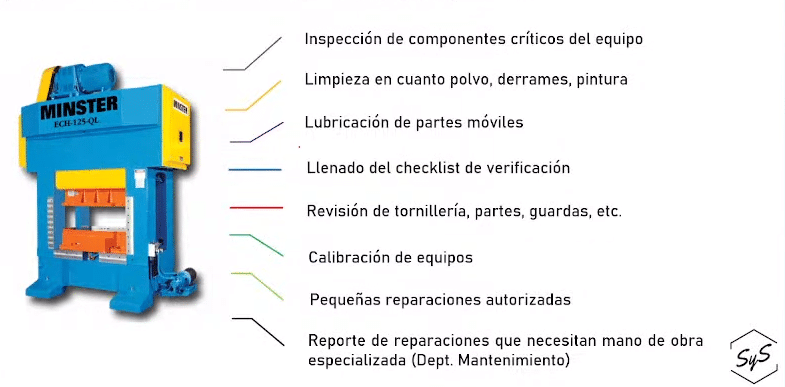
¿Cómo llevar a cabo el TPM?
El TPM puede llevarse a cabo principalmente de dos maneras. Ambas maneras o tácticas de aplicación resultan efectivas si se combinan en la ejecución del TPM.
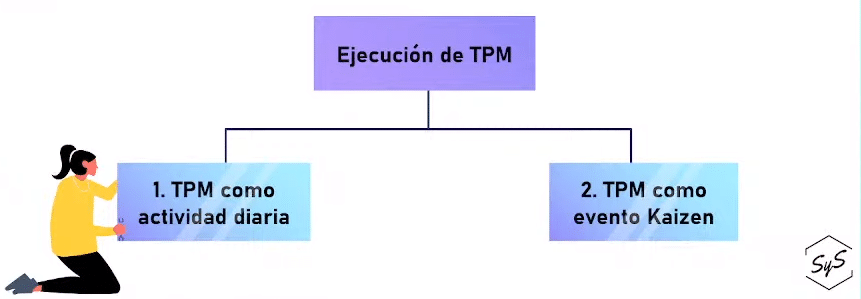
TPM como cultura o actividad diaria
La primera es llevada a cabo de manera rutinaria por el mismo operador:
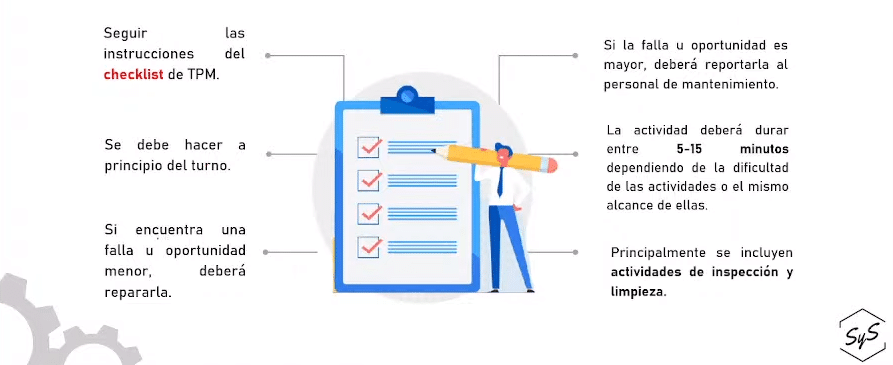
Formato para emplear TPM
Se usa el siguiente formato para emplear TPM, este está conformado por el nombre del equipo, el número activo, el periodo de TPM y la fecha como primera parte. En la parte del cuerpo se usan los títulos de número, actividad y los días de la semana, separado en turnos en caso de tenerlos.
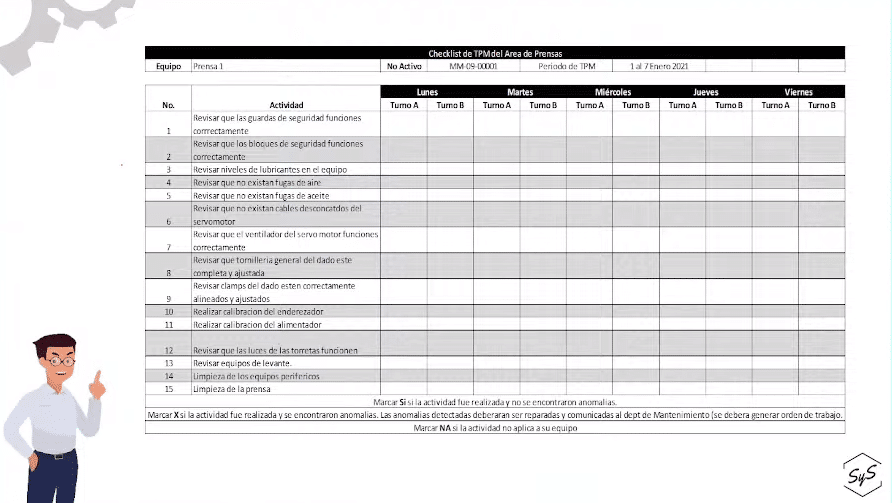
En este formato se colocan los resultados de las actividades realizadas para verificar si todo está en orden.
TPM como evento Kaizen
La segunda es llevada a cabo de manera anual (o semestral dependiendo de la empresa), pero en este caso deberá ser realizada entre el grupo de soporte:
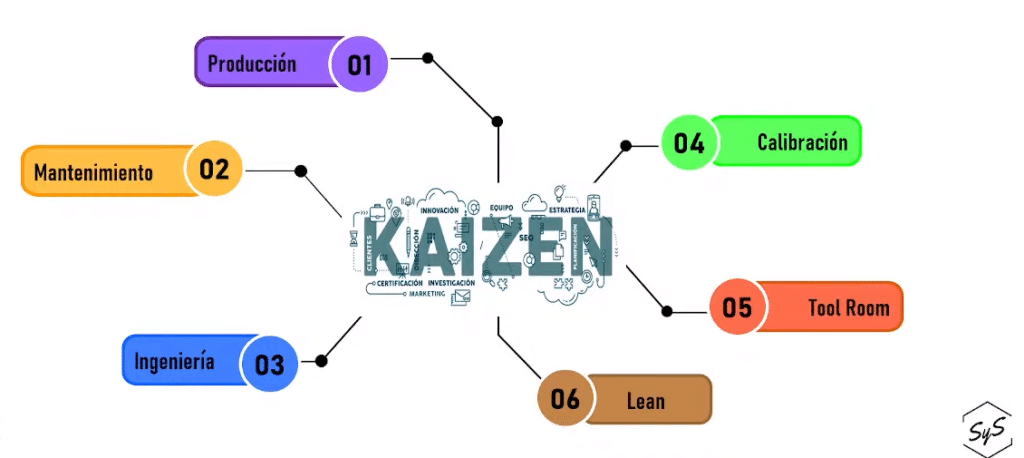
La táctica de Taller de mejora rápida o RIW
Se busca aprovechar un paro planeado del equipo para hacer todas las actividades pendientes:
Limpieza pintura
Mantenimientos Correctivos
Mantenimientos Predictivos
Actualización de equipo
Reparaciones
Mantenimientos Preventivos
Mejoras en la estación de trabajo
¿TPM – Taller de mejora rápida?
Trabajo previo (2-4 semanas) | Semana de trabajo | Seguimiento (4-8 semanas) |
Grupos de trabajo. Entrenamiento en TPM. Identificación y localización de fallas. Cotización y compra de refacciones. Situación actual vs futuro. | Inicio de la actividad Súper limpieza Pintura total Preventivos Correctivos Predictivos Actualizaciones Cierre del Taller. Presentación Final pasado vs. Actual. | Seguimiento a las actividades pendientes. Actualización de documentación de mantenimiento (planes, diagramas, etc.) |
Indicadores de mantenimiento
Costos de mantenimiento
Correctivo
Preventivo
MTTF (Tiempo medio entre fallas)
OEE (Eficiencia Total de equipo)
Rotación de inventario de refacciones
Total de órdenes generadas
Correctivo
Preventivo
Valor de inventario en refacciones
MTTR (Tiempo medio entre reparación)
Si te gustó el contenido, no olvides visitar nuestra página web https://academy.dpsys.com.mx/
para encontrar más temas relacionados con la ingeniería.
¡También podrás encontrar cursos y capacitaciones en distintas áreas que tenemos para ofrecerte!
Escríbenos a nuestro correo contacto@dpsys.com.mx para obtener más información.
¡Te esperamos!