Las industrias viven una ardua carrera en busca de la eficiencia donde es necesario generar y atender una demanda por un producto en el mercado, optimizar al máximo sus procesos para reducir errores, mejorar la calidad, eliminar los desperdicios, reducir costos y riesgos y maximizar la productividad y, consecuentemente, la rentabilidad.
No sólo la competencia entre las industrias, sino el aumento en las exigencias de los clientes, tanto por calidad, como en la atención de plazo de entrega, llevan a las industrias a buscar soluciones y metodologías que las hagan más eficientes. Entre ellas, el más conocido y exitoso modelo es Lean Manufacturing.
DESPERDICIO es todo aquello que no
añade valor al producto, o que no
es absolutamente esencial para
fabricarlo. El valor se añade cuando
las materias primas se transforman del
estado en que se han recibido en otro
estado de un grado superior de acabado
que algún cliente está dispuesto a
comprar.
Tipos de desperdicios
- Transporte
- Sobreproducción
- Tiempo de espera
- Exceso de procesos
- Inventario
- Defectos en el producto
- Movimientos
- Personal subutilizado
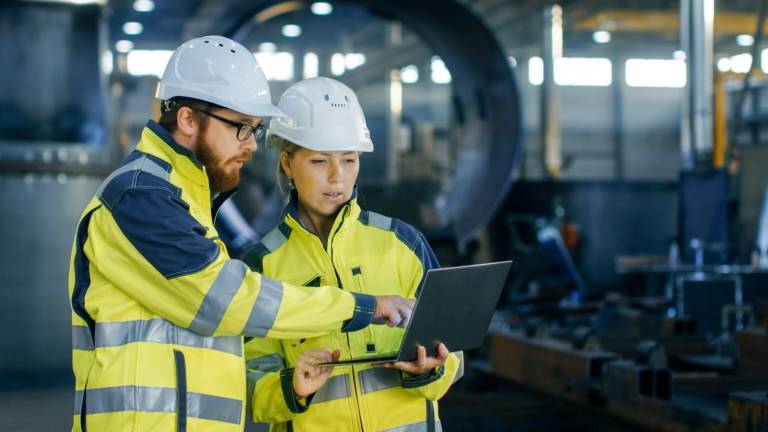
Transporte
El desperdicio por transporte es el resultado de un movimiento o manipulación de material innecesario. Las máquinas y las líneas de producción deberían estar lo más cerca posible y los materiales deberían fluir directamente desde una estación de trabajo a la siguiente sin esperar en colas de inventario. Hay que optimizar la disposición de las máquinas y los trayectos de los suministradores.
Cuantas más veces se muevan los artículos de un lado para otro mayores son las probabilidades de que resulten dañados. Resumiendo, tenemos que evitar mover las piezas por la planta, de un proceso a otro y gente que ande por la planta buscando herramientas o moviendo materiales. Cabe aclarar que nos referimos en este caso al transporte dentro de las instalaciones de la empresa, y no a la entrega del producto a los clientes o centros de distribución.
Características
- Los contenedores son demasiado grandes, o pesados, difíciles de manipular.
- Exceso de operaciones de movimiento y manipulación de
materiales. - Los equipos de manutención circulan vacíos por la planta.
Causas posibles
- Layout obsoleto.
- Gran tamaño de los lotes.
- Procesos deficientes y poco flexibles.
- Programas de producción no uniformes.
- Tiempos de preparación elevados.
- Excesivos almacenes intermedios.
- Baja eficiencia de los operarios y las máquinas.
- Reprocesos frecuentes.
Sobreproducción
El desperdicio por sobreproducción es el resultado de fabricar más cantidad de la requerida o de invertir o diseñar equipos con mayor capacidad de la necesaria. La sobreproducción es un desperdicio fatal porque no incita a la mejora, ya que parece que todo funciona correctamente.
Significa perder tiempo en fabricar un producto que no se necesita, representa un consumo inútil de material, se incrementan los transportes internos y se llenan de stock los almacenes. Así pues, el desperdicio de la sobreproducción es como una llave que abre la puerta a otras clases de desperdicio.
Características
- Gran cantidad de stock.
- Equipos sobredimensionados.
- Flujo de producción no balanceado o nivelado.
- Presión sobre la producción para aumentar la utilización.
- No hay prisa para atacar los problemas de calidad.
- Tamaño grande de los lotes de fabricación.
- Excesivo material obsoleto.
- Necesidad de espacio extra para almacenaje.
Causas posibles
- Procesos no capaces.
- Pobre aplicación de la automatización.
- Tiempos de cambio y de preparación demasiado largos.
- Procesos poco fiables.
- Programación inestable.
- Respuesta a las previsiones, no a las demandas.
- Falta de comunicación.
Tiempo de espera
El desperdicio por tiempo de espera es el tiempo perdido como resultado de una secuencia de trabajo o proceso ineficiente. Los procesos establecidos pueden provocar que unos operarios permanezcan parados mientras otros están saturados de trabajo. Un cliente nunca estará dispuesto a pagar el tiempo perdido durante la fabricación de su producto, así que es preciso estudiar cómo utilizar estos tiempos o bien cómo eliminarlos.
Características
- El operario espera a que la máquina termine.
- La máquina espera a que el operario acabe una tarea
pendiente. - Un operario espera a otro operario.
- Exceso de colas de material dentro del proceso.
- Paradas no planificadas.
- Tiempo para ejecutar otras tareas indirectas.
- Tiempo para ejecutar reproceso.
Causas posibles
- Métodos de trabajo poco consistentes.
- Layout deficiente por acumulación o dispersión de procesos.
- Desequilibrios de capacidad.
- Producción en grandes lotes.
- Pobre coordinación entre operarios y/o entre operarios y
máquinas. - Tiempos de preparación de máquina o cambios de utillajes
complejos. - Falta de maquinaria apropiada.
- Operaciones “caravana”: falta personal y los operarios
procesan lotes en más de un puesto de trabajo. - Operaciones retrasadas por omisión de materiales o piezas.
Sobreproceso
El desperdicio por sobreproceso es el resultado de poner más valor añadido en el producto que el esperado o el valorado por el cliente, en otras palabras, es la consecuencia de someter al producto a procesos inútiles, por ejemplo: verificaciones adicionales, aplicaciones innecesarias de pintura, algunos trabajos de limpieza, etc.
El objetivo de un proceso productivo debería ser obtener el producto acabado sin aplicar más tiempo y esfuerzo que el requerido. En las
empresas de servicios estos despilfarros se manifiestan en procesos administrativos burocráticos, innecesariamente complejos o pesados.
Características
- No existe estandarización de las mejores técnicas o procedimientos.
- Maquinaria mal diseñada o capacidad calculada incorrectamente.
- Aprobaciones redundantes o procesos burocráticos inútiles.
- Excesiva información (que nadie utiliza y que no sirve para nada).
- Falta de especificaciones y ejemplos claros de trabajo.
Causas posibles
- Cambios de ingeniería sin cambios de proceso.
- Toma de decisiones a niveles inapropiados.
- Procedimientos y políticas no efectivos.
- Falta de información de los clientes con respecto a los requerimientos.
Exceso de inventario
Los stocks son la forma de despilfarro más clara porque esconden ineficiencias y problemas crónicos. Como consecuencia de sus
relaciones con estos problemas, los directores japoneses han denominado al stock la “raíz de todos los males”.
Desde la óptica JIT, los inventarios se contemplan como los síntomas de una fábrica enferma, de la misma manera que los médicos observan
como síntomas típicos de la gripe, la fatiga, la fiebre y el malestar general,
los doctores JIT ven a los stocks como los síntomas de la mala salud en las operaciones de una fábrica.
Algunos argumentos para considerar los stocks como síntomas
de una enfermedad son los siguientes:
• Encubren los stocks muertos que generalmente, se detectan
una vez al año, cuando se realizan los inventarios físicos. Se trata de
productos y materiales que no sirven para nada porque son obsoletos, caducados, rotos, etc., pero que no se han dado de baja.
• Los stocks necesitan cuidados, mantenimiento, vigilancias,
contabilidad, gestión etc.
• Agobian las partidas de los activos de los balances, principalmente las del activo corriente. La expresión “inversión en stocks” es un error, porque no ofrecen retribución sobre las inversiones y por tanto no pueden ser considerados como tales en ningún momento. También agobian las partidas del inmovilizado material si son necesarias instalaciones de almacenamiento automático o inteligente.
El despilfarro por stock es el resultado de tener mayor cantidad de existencias de las necesarias para satisfacer las necesidades más inmediatas. El hecho de que se acumule material antes y después del proceso indica que hay stock innecesario y que el flujo de producción no es continuo.
En este caso, se deberían monitorizar las actividades intermedias para
identificar y resolver el problema.
Características
- Excesivos días con el producto acabado o semielaborado.
- Grandes costes de movimiento y de mantenimiento o posesión del stock.
- Excesivo equipo de manipulación (carretillas elevadoras, etc.).
- Excesivo espacio dedicado al almacén.
- Containers o cajas demasiado grandes.
Causas posibles
- Procesos con poca capacidad.
- Cuellos de botella no identificados o incontrolados.
- Proveedores no capaces.
- Tiempos de cambio de máquina o de preparación de trabajos
excesivamente largos. - Previsiones de ventas erróneas.
- Decisiones de la dirección general de la empresa.
- Retrabajo (volver a procesar algo por segunda vez) por defectos de calidad del producto.
- Problemas e ineficiencias ocultas.
Defectos
El despilfarro derivado de los errores es uno de los más aceptados en la industria, aunque significa una gran pérdida de productividad, porque incluye el trabajo extra que debe realizarse como consecuencia de no
haber ejecutado correctamente el proceso productivo la primera vez.
Los procesos productivos deberían estar diseñados a prueba
de errores para conseguir productos acabados con la calidad exigida, eliminando así cualquier necesidad de retrabajo o de inspecciones adicionales. También debería haber un control de calidad en tiempo real de modo que los defectos en el proceso productivo se detecten justo cuando suceden, minimizando así el
número de piezas sospechosas que requieren inspección adicional y/o repetición de trabajos.
Características
- Pérdida de tiempo, recursos materiales y dinero.
- Planificación inconsistente.
- Calidad cuestionable.
- Flujo de proceso complejo.
- Recursos humanos adicionales para operaciones de inspección y repetición de trabajos.
- Espacio y herramientas extra para el retrabajo.
- Maquinaria poco fiable.
- Baja moral de los operarios.
Causas posibles
- Disposición de maquinaria inadecuada o ineficiente.
- Proveedores o procesos no capaces.
- Errores de los operarios.
- Entrenamiento y/o experiencia del operario inadecuada.
- Herramientas o utillajes inadecuados.
- Proceso productivo deficiente.
Movimientos innecesarios
El desperdicio por movimientos innecesarios es el resultado de desplazamientos, ya sean de personas o equipamiento, que no añada valor al producto. Por ejemplo, personas subiendo y bajando a por documentos, buscando herramientas, caminar innecesariamente, etc.
Todo esto provoca un aumento del cansancio de los operarios, con los consiguientes problemas de salud, y una disminución del tiempo dedicado
a lo que realmente aporta valor.
Personal subutilizado
No saber asignar a cada persona en el puesto que se adapte mejor a sus aptitudes o no apostar por la formación continua del personal conlleva aminorar notablemente la tendencia de mejora.
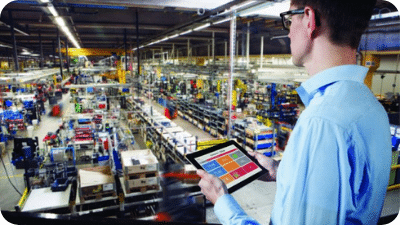
Herramientas para evitar los Desperdicios
Value Stream Mapping (VSM)
El VSM es el Mapa de la Cadena de Valor, y es un modelo gráfico que representa la cadena de valor de un proceso de fabricación, mostrando tanto el flujo de materiales como el flujo de información desde el proveedor hasta el cliente a través de todas sus actividades. El VSM ayuda a entender, de manera visual y simple, un proceso con todas sus actividades, y a identificar los posibles desperdicios o actividades que no aportan valor añadido con el fin de eliminarlas y ganar en productividad.
Aunque inicialmente, esta herramienta se ha utilizado en los procesos de fabricación industrial, también se puede aplicar en procesos que no son de fabricación, y de hecho se está aplicando. Simplemente hay que adaptar los conceptos al tipo de proceso analizado.
5S
Esta herramienta se utiliza para conseguir mejorar las condiciones de trabajo de cada puesto y que el orden y la limpieza se mantengan permanentemente, eliminando desperdicios y estandarizando las mejores prácticas que ayudan a realizar un “buen trabajo”. Las 5S provienen de términos japoneses y son: Clasificar (Seiri), Ordenar (Seiton), Limpieza (Seiso), Estandarizar (Seiketsu), Disciplina (Shitsuke).
TPM (Total Productive Maintenance)
Es una serie de métodos para asegurar que cada componente del equipo (máquinas y herramientas), en un proceso de producción, siempre sea capaz de realizar las tareas requeridas para que la producción nunca sea interrumpida, que no haya averías ni paradas no previstas. La idea fundamental es que la mejora y buena conservación de los equipos productivos es una tarea que debe involucrar a todos.
Kanban
Es una herramienta para el control del flujo de producción basado principalmente en tarjetas, aunque se pueden utilizar otro tipo de señales. Con esta técnica se trabaja con un sistema Pull respecto a las necesidades del cliente para producir la cantidad necesaria en el momento adecuado.
Six Sigma
Es una metodología de mejora de procesos, centrada en la reducción de la variabilidad de los mismos, consiguiendo reducir o eliminar los defectos o fallos en la entrega de un producto o servicio al cliente. La meta de 6 Sigma es llegar a un máximo de 3,4 defectos por millón de eventos u oportunidades, entendiéndose como defecto cualquier evento en que un producto o servicio no logra cumplir los requisitos del cliente.
Reingeniería
Consiste en el rediseño de los procesos para que éstos tengan un rendimiento radicalmente diferente. Se trata de cuestionar todos los aspectos relacionados de un proceso, sus outputs, actividades, tecnología empleada, recursos, estructura y objetivos.
Ciclo PDCA de Mejora Continua
El análisis mediante el ciclo de calidad PDCA es una de las técnicas fundamentales para analizar y corregir defectos y/o desperdicios. Esta técnica es la base para llevar a cabo todo el proceso de mejora continua.
Las 7 herramientas básicas de la calidad
Son un conjunto de técnicas gráficas identificadas como muy útiles en la solución de problemas relacionados con la calidad. Estas 7 técnicas son el Diagrama Causa-Efecto, el Diagrama de líneas, el Histograma, el Diagrama de Pareto, las Listas de Chequeo o Verificación, los Gráficos de Control y los Gráficos de Dispersión.
Kaizen
Filosofía de trabajo mediante la cual todos los empleados trabajan conjuntamente para mejorar de manera continua. Está relacionada con los grupos y equipos de mejora.