El día miércoles 01 de Junio, el ingeniero Yussef Salomón impartió el taller sobre la Metodología 5’S, en la cual habló sobre su objetivo, su definición, por qué se usa, cada una de las “S” y los beneficios de implementarla.
Objetivo
La producción Lean es un modelo de gestión que se enfoca en minimizar las pérdidas de los sistemas de manufactura al mismo tiempo que maximiza la creación de valor para el cliente final. Para ello utiliza la mínima cantidad de recursos, es decir, los estrictamente necesarios para el crecimiento.
¿Qué son las 5’S?
La metodología 5’S se creó en Toyota, en los años 60 y agrupa una serie de actividades que se desarrollan con el objetivo de crear condiciones de trabajo que permitan la ejecución de crear condiciones de trabajo que permitan la ejecución de labores de forma organizada, ordenada y limpia. Dichas condiciones se crean a través de reforzar los buenos hábitos de comportamiento e interacción social, creando un entorno de trabajo eficiente y productivo.
La metodología de las 5’S es de origen japonés, y se denomina de tal manera, ya que la primera letra del nombre de cada una de las etapas es la letra “S”.
Principios de la metodología
Esta metodología se compone de cinco principios fundamentales:
- SEIRI: Clasificación u organización
- SEITON: Orden
- SEISO: Limpieza
- SEIKETSU: Estandarización
- SHITSUKE: Disciplina
Objetivos específicos
- Mejorar y mantener las condiciones de organización, orden y limpieza en el lugar de trabajo.
- A través de un entorno de trabajo ordenado y limpio, se crean condiciones de seguridad, de motivación y de eficiencia.
- Eliminar desperdicios de la organización.
- Mejorar la calidad de la organización.
¿Por qué las 5’S?
Es una técnica que se aplica en todo el mundo con excelentes resultados por su sencillez y efectividad.
Su aplicación mejora los niveles de:
- Calidad
- Eliminación de tiempos muertos
- Reducción de costos
La aplicación de esta técnica requiere de compromiso personal y duradera para que la empresa sea un auténtico modelo de organización, limpieza, seguridad e higiene.
Las 5’s
1ra – Clasificación (SEIRI)
Consiste en identificar y clasificar los materiales indispensables para la ejecución del proceso. El resto, se considera material innecesario y por lo tanto se eliminará o separará. A partir de ese momento, se realizará un inventario estándar para cada puesto de trabajo.
Ventajas de clasificación y descarte:
- Reducción de necesidades de espacio, stock, almacenamiento, transporte y seguros.
- Evita la compra de materiales no necesarios y su deterioro.
- Aumenta la productividad de las máquinas y personas implicadas.
- Provoca un mayor sentido de la clasificación y la economía, menor cansancio físico y mayor facilidad.
Para poner el práctica la 1er S, debemos hacernos las siguientes preguntas:
- ¿Qué debemos tirar?
- ¿Qué debe ser guardado?
- ¿Qué puede ser útil para otra persona u otro departamento?
- ¿Qué debemos reparar?
- ¿Qué debemos vender?
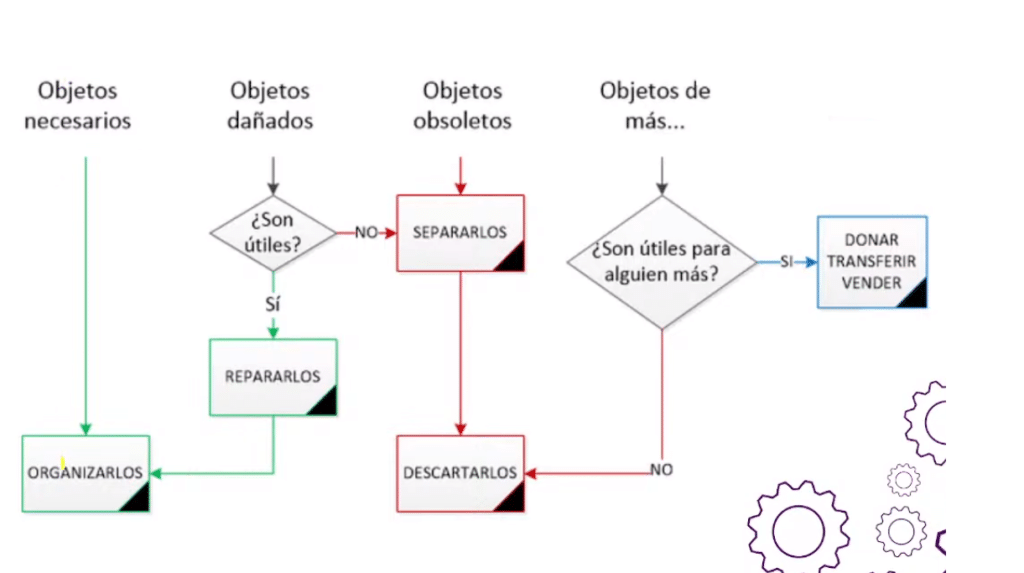
2da – Organización (SEITON)
En segundo lugar, se produce a ordenar los materiales indispensables, facilitando las tareas de encontrar, usar y responder estos útiles.
Con ello, se consigue eliminar tiempos no productivos asociados a la búsqueda de materiales y desplazamientos innecesarios. Se debe marcar la ubicación, de cada material, componente o herramienta, para ellos nos servimos de etiquetas, moldes, dibujos, señales, etc.
Para tener claros los criterios de colocación de cada cosa en su lugar adecuado, se deben responder las siguientes preguntas:
- ¿Es posible reducir el stock de esta cosa?
- ¿Esto es necesario que esté a la mano?
- ¿Todos llamaremos a esto con el mismo nombre?
- ¿Cuál es el mejor lugar para cada cosa?
Por último hay que tener en claro que:
- Todas las cosas han de tener un nombre y todos deben conocerlo
- Todas las cosas deben tener espacio definido para su almacenamiento o colocación, indicando con exactitud y conocido también por todos
3ra – Limpieza (SEISO)
Para conseguir que la limpieza sea un hábito, se deben tener en cuenta los siguientes puntos:
- Todos deben limpiar utensilios y herramientas al terminar de usarlas y antes de guardarlas.
- Las mesas, armarios y muebles deben estar limpios y en condiciones de uso.
- No debe tirarse nada al suelo
- No existe ninguna excepción cuando se trata de limpieza.
Analice por un momento su lugar de trabajo y responda:
- ¿Cree que realmente puede considerarse como “limpio”?
- ¿Cómo cree que podría mantenerlo limpio siempre?
- ¿Qué utensilios, tiempo o recursos necesitaría para ello?
- ¿Qué cree que mejoraría el grado de limpieza?
4ta – Estandarizar (SEIKETSU)
El proceso de estandarizar trata de distinguir fácilmente una situación “normal” de una “anormal”, es decir, el personal debe ser capaz de discernir cuando las tres eses anteriores se están aplicando correctamente y cuando no.
Es imprescindible que todo el personal de planta disponga de la formación adecuada para identificar este tipo de situaciones. De esta forma, el personal se siente más valorado y aumenta su motivación. A su vez, los operarios son más polivalentes y son capaces de detectar pequeños fallos en su puesto, que posteriormente pudieran desencadenar problemas más graves.
Hay que recordar que estos avisos y recordatorios:
- Deben ser visibles a cierta distancia.
- Deben colocarse en los sitios adecuados.
- Deben ser claros, objetivos y de rápido entendimiento.
- Deben contribuir a la creación de un local de trabajo motivador y confortable.
Analice por un momento su lugar de trabajo y responda:
- ¿Qué tipo de carteles, avisos, advertencias, procedimientos cree que faltan?
- ¿Los que ya existen son adecuados?, ¿proporcionan seguridad e higiene?
- En general, ¿calificaría su entorno de trabajo como motivador y confortable?
- En caso negativo, ¿cómo podría colaborar para que si lo fuera?
5ta- Disciplina (SHITSUKE)
Las 5’S no tienen un fin definido. Es un ciclo que se repite continuamente y en el que se debe disponer de una disciplina para mantener un puesto de trabajo ordenado y limpio.
El éxito en la implementación de las 5’S, genera un espacio de trabajo mucho más agradable, se reducen stocks, accidentes y se aumenta la productividad y satisfacción del personal de la empresa. Por ello, la prioridad es mantener esa disciplina de una forma rigurosa y constante.
Beneficios de las 5’S
- La implementación de las 5’S se basa en el trabajo en equipo
- Los trabajadores se comprometen.
- Se valoran sus aportaciones y conocimiento.
- La mejora se hace una tarea de todos.
Se consigue una mayor productividad, lo que se traduce en:
- Menos productos defectuosos
- Menos averías
- Menor nivel de existencias o inventarios
- Menos accidentes
- Menos movimientos y traslados inútiles
- Menor tiempo para el cambio de herramientas
Si te gustó el contenido, no olvides visitar nuestra página web https://academy.dpsys.com.mx/
para encontrar más temas relacionados con la ingeniería.
¡También podrás encontrar cursos y capacitaciones en distintas áreas que tenemos para ofrecerte!
Escríbenos a nuestro correo contacto@dpsys.com.mx para obtener más información.
¡Te esperamos!